Hydrogen’s role in the global energy transition requires a deep understanding of its unique properties to ensure safe handling and effective risk mitigation. Like more familiar fuels such as natural gas, hydrogen exhibits behaviours that significantly influence its safety profile, but these are different to hydrocarbons, requiring specific strategies to manage the associated physical and chemical hazards.
One such chemical hazard is hydrogen’s wide flammability range, 4% to 75% by volume, significantly wider that of natural gas, which ignites within a narrower 5% to 15% range (Fig. 1). As a result, hydrogen can more readily form flammable mixtures in air, heightening the risk of ignition upon release. Additionally, the energy required to ignite hydrogen is very low – only 0.017 millijoules (mJ), compared to the 0.290 mJ needed for natural gas. This means even low energy sources such as static sparks (0.5 mJ) can result in a hydrogen explosion. One recent green hydrogen loss (Ref. 1) was caused by ignition due to static electricity as proper earthing connections were missing. Hydrogen also has the potential for spontaneous ignition due to the unusual reverse Joule-Thomson effect (unlike other gases compressed hydrogen at ambient temperature will heat up on expansion to atmospheric pressure).
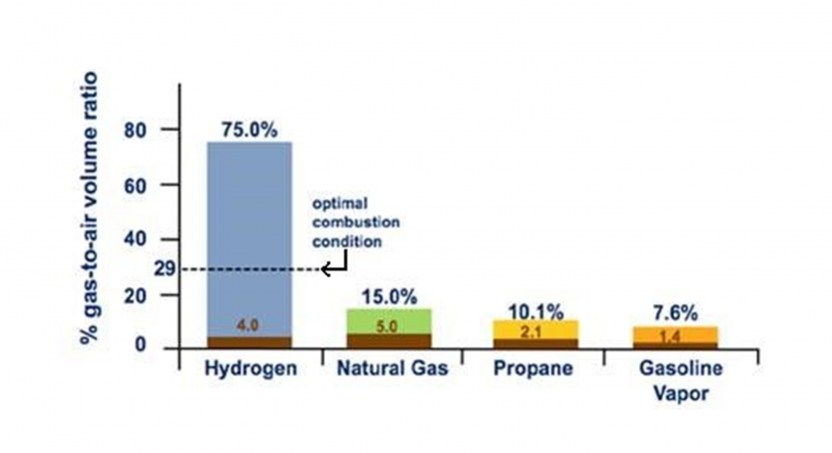
Hydrogen’s flame velocity, measured at 3.2 m/s, is eight times faster than that of natural gas. This leads to a significantly higher potential for explosive pressure buildup, the so-called Deflagration to Detonation Transition (DDT), which is promoted by turbulence and congestion. In the event of ignition, the resulting explosion could be far more severe than one involving natural gas, with detonation overpressures which can reach 100 times that of the deflagration case, resulting in significant Property Damage (PD). Robust containment and mitigation strategies are therefore required. Hydrogen’s low density and high diffusivity also mean that under similar conditions, it flows out of leaks 3.8 times faster than natural gas, leading to rapid depressurization and potentially larger flammable clouds. If ignited, hydrogen burns quickly, with a smokeless flame almost invisible to the naked eye. Its radiant heat is low (10% that of natural gas) with a high flame temperature (> 2000C). These characteristics result in a fire of shorter duration, whilst increasing the flame intensity and immediate danger.
Hydrogen’s unique fire and explosion risks therefore require stringent loss control measures to prevent accidental ignition. Despite these risks, hydrogen’s rapid dispersion into the atmosphere – thanks to its low molecular weight and high buoyancy– can reduce the likelihood of hazardous gas clouds accumulating at ground level. This characteristic does not however eliminate the risk of ignition, especially in confined spaces such as electrolyser halls where hydrogen can accumulate at the apex.
Physical hazards include unique hydrogen-induced damage mechanisms. These mechanisms include hydrogen embrittlement (HE), high-temperature hydrogen attack (HTHA), hydrogen blistering, hydrogen-induced cracking (HIC), and hydrogen stress cracking (HSC), and these impact the mechanical properties of a component, such as tensile strength, fracture toughness, fatigue life, crack propagation rate leading to eventual failure. HTHA is not usually a problem for electrolyser systems other than Solid Oxide Electrolysers (SOECs) as it requires temperatures > 200C. However, hydrogen embrittlement is a known failure mechanism, particularly at ambient temperatures and with high cyclic stress and higher-pressure operations, typical of pressurised electrolyser systems. HE damage can be avoided by correct material selection and correct welding techniques, thereby avoiding circumstances that could lead to a major leak or failure of equipment or piping. Regular inspections and proactive maintenance play a pivotal role in preventing equipment failures that could lead to hazardous situations. Non-destructive testing (NDT) such as ultrasonic, acoustic emissions and electromagnetic techniques can be used to detect defects associated with these damage mechanisms. Routine inspection of hydrogen joints (flanges, threaded fittings, welds) can be performed using the latest leak testing methodology to mitigate this risk.
Green Hydrogen - Safety in Design
For Risk Engineers carrying out green hydrogen risk assessments for insurance purposes during construction and operational phases, identifying whether the insured has carried out an identification of safety vulnerabilities is key. The following safety related studies should be key deliverables from FEEDOverall Safety Philosophy;
- Fire and Explosion Risk Assessment Report;
- Quantitative Risk Assessment (QRA);
- Fire and Gas Detection System Design;
- Hazardous Area Classification Drawings;
- Firewater System Demand Calculations and Design;
- Vent Dispersion and Radiation Studies;
- HAZID Report;
- HAZOP Report;
- Safety Integrity Level (SIL) Report
Prevention/Control and Mitigation Measures
Safe deployment of hydrogen technologies requires robust design philosophies that systematically address potential hazards. This approach ranges from eliminating risks to managing the consequences of incidents, through a series of barriers or layers of protection.
- Avoidance – eliminating hazards: The most effective safety strategy is to eliminate hazards altogether through inherently safe design. As hydrogen projects increase in scale, large quantities will be produced, stored and transported. Design strategies focus on reducing the presence of hydrogen in vulnerable areas, such as reducing storage quantities in high-risk zones, minimising gas hold-up volumes in electrolyser stacks and piping, spacing of containerised electrolysers, or segregation of electrolyser halls.
- Prevention – reducing the likelihood of a Loss of Containment (LoC): The next line of defence after minimizing flammable inventories is prevention – reducing the likelihood of hydrogen escaping its containment. This involves rigorous engineering design, high-quality materials, cell and stack condition monitoring, and adherence to stringent industry standards to ensure hydrogen remains securely contained, reducing the risk of leaks. Organizations such as ISO, NFPA and CEN are at the forefront of creating technical guidelines that ensure the safe and efficient use of hydrogen, including standards for electrolyser design for both indoor and outdoor use. Some of the key design considerations include:
Proper ventilation of any hydrogen enclosures is important to keep hydrogen concentrations below lower flammability levels. The typical six air changes per hour used for other hazardous gases may not be enough for hydrogen applications. Ventilation design should have air inlets at the lowest point, with outlets at the highest point, where hydrogen can accumulate. Where forced ventilation is used, non-sparking fans and electronics should be specified for ignition source control. Failure or shutdown of ventilation systems should be interlinked to shutdown and venting of the hydrogen production equipment.
Electrical equipment located near hydrogen production equipment or piping should have appropriate hazardous area classification. Electrical components should follow Class 1, Division 1 or 2, Group B of the NEC code or as required by ATEX code to define extents and distance round equipment.
General layout principles include providing sufficient separation distances to minimise escalation of an initiating event, maximising open structures to avoid accumulation and to facilitate dispersion of flammable vapours, decreasing the degree of congestion and confinement to minimise overpressures. Minimum separation distances that are provided in both NFPA 2 and NFPA 55 codes consider unignited releases and ignited jet flames of hydrogen at various pressures.
- Control – limiting the scale and duration of LoC events: Despite the best preventive efforts, the possibility of a hydrogen leak cannot be ruled out. Control measures are therefore critical, involving strategies such as gas detection systems, venting and emergency shutdown procedures that rapidly isolate the affected area, preventing a small leak from escalating into a catastrophic event. There are a variety of technologies to detect hydrogen leaks including conventional catalytic bead, thermal, acoustic and palladium film. These are all types of point gas detector and need to be located close to and above the location where the leak is likely to occur. Other point detection methods include hydrogen leak detection tape, which changes colour on contact with hydrogen. Standard line-of-sight detectors that rely on infrared (IR) absorption typically won't detect hydrogen directly. The only line of sight technology available for detection of hydrogen gas is Open-Path Tunable Diode Laser Absorption Spectroscopy.
Hydrogen burns with a unique electromagnetic signature, meaning that traditional flame detectors designed for hydrocarbon fires are unsuitable for hydrogen. Multi spectrum infra-red (MIR) detectors are a novel point detection technology sensitive to a wide range of IR wavelengths including those emitted by water vapour in hydrogen flames. These detectors are superior to combined UV/IR detectors which tend to result in more false alarms being sensitive to arcs, welding, lightning and other UV-rich sources. Thermal heat detectors rely on the heat radiation emitted by the hydrogen flame. Distributed optical fibre is an innovative and effective heat detection technology and relies on measuring heat distribution along the optical fibre cable using the fibre itself as a sensor.
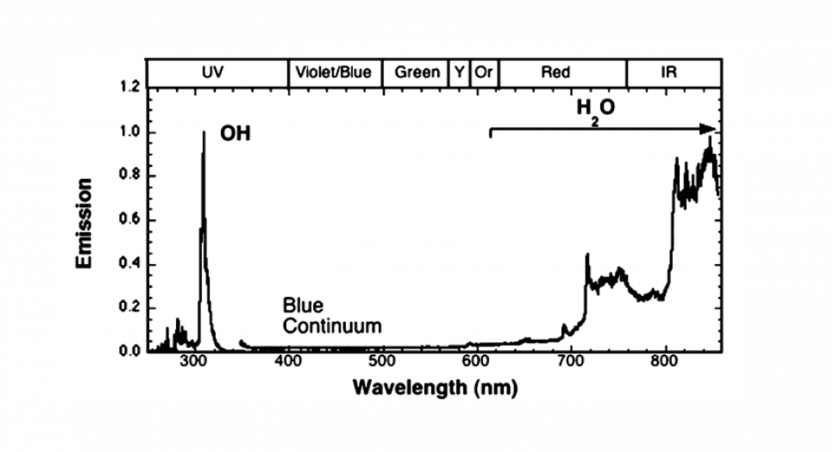
These hydrogen-specific fire & gas detection systems initiate necessary actions to safeguard personnel and equipment including active fire protection, closing fire dampers, and initiation of ESD shutdown levels.
Mitigation – protecting people and assets: Mitigation focuses on reducing the impact of incidents when they occur. This includes installing protective barriers, implementing ventilation systems to disperse hydrogen, isolation and shutdown, using fire-resistant materials to shield assets, deployment of active fire protection. Effective emergency response protocols are also crucial, ensuring coordinated efforts to contain any damage. Automatic shutdown procedures are implemented to halt the flow of hydrogen and depressurise equipment, preventing further leakage and mitigating the risk of an incident. Discharges of hydrogen must be released to the atmosphere through a vent system at a sufficient height and safe location, reducing the risk of hazardous accumulation and potential explosions. Depending on the location and on the possibility of being impacted by blast waves due to explosion, buildings should be designed explosion-resistant and/or fire resistant, to withstand a design level blast overpressure and/or thermal radiation level they could experience. The need for active fire protection will be justified based on the outcome of a safety review after identifying the type of fire hazard present. High pressure hydrogen releases can result in jet fires. The unique characteristics of hydrogen combustion, such as its high flame temperature, high emissive power and rapid heat release, contribute to the broader thermal radiation contours observed in these scenarios. Tests on bare steel show that the core temperature can reach 400C in less than 1 minute, less than half the time of a standard jet fire thereby risking failure of impinged piping or structures. A new flexible epoxy intumescent Passive Fire Protection (PFP) coating has been recently tested in high pressure erosive hydrogen jet fire environments. When exposed to the high temperatures of the fire, the PFP expands to form a robust, insulating char that significantly reduces the rate of heat up of the protected item, allowing time for active fire protection systems to come online. The plant firewater system should be supplied by a secure and reliable water supply which should include items such as backup electric pumps where appropriate.
Lessons Learned from Industry Losses
Accident and incident databases are important tools for identifying hazards in specific processes. Several loss databases already exist for hydrogen: USDOE Hydrogen Incident Reporting Database, UKHSE Major Hazard Incident Database Service and The Centre for Hydrogen Safety which maintains the https://h2tools.org/ website for sharing lessons learned from hydrogen related safety events, and which was combined with the Hydrogen Safety Best Practices database in 2009. The Hydrogen Incidents and Accidents (HIAD) Database is one of the largest collections for hydrogen specific data including electrolysis-related incidents.
These databases show that in rare scenarios hydrogen and oxygen can mix and given the right conditions lead to an explosion as happened at Laporte Industries in Ilford in 1975 (Ref 2). In this event there was a flammable mixture buildup in the oxygen header due to differential pressure, resulting in a DDT event taking place in the oxygen filter vessel.
Other potential Expected Maximum Loss (EML) events include hydrogen leakage leading to accumulation within a building, resulting in a confined in-building explosion (VCE), or a release and explosion outside a building in a highly congested area. There is the risk of a domino effect: in the event of a fire and explosion in one stack or module this could have an impact on adjacent modules.
Whilst jet fires and flash fires due to ignition of hydrogen releases will lead to property damage, hydrogen explosion events will be an EML event. Various industry models are being developed to assess the overpressure and damage circles resulting from an explosion following a hydrogen release, accounting for congestion and level of confinement, and to determine safety distances. These include the TNT Multi-Energy Model (MEM) and the Baker-Strehlow-Tang (BST) method. The former uses degrees of congestion in determining the initial blast strength, while the latter is based on specification of a Mach number and sometimes underpredicts the explosion overpressure. These models have been validated for hydrocarbons; further validation will be required against experimental datasets for hydrogen in order to lend an appropriate degree of confidence to damage modelling. Baker Risk and DNV and others are actively involved in hydrogen explosion modelling to validate these methods for both confined and unconfined explosions (Ref. 5).
Detonation (DDT) may be considered as a scenario for larger clouds. Although the mass of hydrogen released in a green hydrogen loss event is likely to be significantly less than, for instance, a propane VCE, the damage caused can be significant. For instance, a containerised PEM electrolyser (2 x 2.5 MW stacks), produces 1,000 Nm3/hr (90 kg/hr) of hydrogen at 30 barg. A 10-minute full bore outlet header leak would result in a cloud size of 15kg. This release is similar in size to the loss that occurred at the Polysar Styrene Plant explosion (Ref 3), in Sarnia, Ontario in 1984 where failure in a compressor flange in an open-sided shed released approximately 30 kg of hydrogen gas. Operating at around 48 barg, the pressurised hydrogen leak quickly accumulated in the compressor shed and exploded after finding an ignition source, causing damage to buildings up to 150m away. A similar loss, involving the release of 10-20kg of hydrogen at the Porsgrunn ammonia plant in 1985 (Ref. 4) resulted in a violent hydrogen-air explosion. It is likely that the gas cloud detonated. The explosion destroyed the building and windows were broken at a distance of over 700m from the centre of the explosion.
These examples are two of the largest industrial hydrogen explosions on record. With scale-up to a 100 MW green hydrogen asset, consisting of 10 arrays in an electrolyser hall, where larger piping headers and downstream gas purification is sized for system level, the cloud size could be 20 x larger than these examples at 300kg, increasing the potential property damage if ignited.
Conclusions
This whitepaper underscores the need for rigorous safety procedures in hydrogen handling, particularly during start-ups and maintenance. It highlights the importance of robust leak detection, strict inspection regimes, and thorough training for managing hazardous gases.
As hydrogen use grows, both industrially and as a cleaner energy source, incidents like those referenced here remind us of the essential role of process safety and continual improvements in engineering standards.
References
[1] AWE Pilot Plant explosion, Gangneung, South Korea, 23 May 2019.
[2] https://www.icheme.org/media/13690/the-explosion-at-laporte-industries-ilford.pdf
[3] Polysar hydrogen explosion in Litol unit, April 1984.
[4] Porsgrunn ammonia plant hydrogen explosion, 1985.
[5] DNV, Application of Phast and Safeti to Hydrogen Consequences and Risks, February 2022